- Szczegóły
- Opublikowano: czwartek, 25 sierpień 2022 07:37
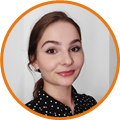
Marta Soczyńska
Odpowiada za dział marketingu i dokłada swoją cegiełkę w sprzedaży produktów firmy Profesal.
Wskaźniki efektywności UR
We współczesnych przedsiębiorstwach prezesi i kierownicy firm nastawieni są na rozwój i ciągłe doskonalenie. Jak jednak określać sobie nowe cele nie mierząc dotychczasowych osiągnięć? Bez pomiarów założenia mogą nie przybliżyć nas do wykonania ustalonej strategii. Dlatego, tak ważna jest analiza wskaźników. Jakie wskaźniki mierzyć, aby móc wyciągać zadowalające wnioski?
Co można mierzyć?
Najczęściej powtarzaną poradą jest „ustal odpowiednie KPI (Kluczowe wskaźniki efektywności) dla twojej firmy i trzymaj się ich jak drogowskazu”. To jednak nie takie proste, w szczególności, że na każdym szczeblu, w każdym dziale, wskaźniki mogą się od siebie znacząco różnić. Początkowo należy określić, co jest dla nas największą bolączką i w jakich obszarach wiemy, że możemy się doskonalić. Następnie, wziąć dwa głębokie oddechy i spojrzeć na swój dział/przedsiębiorstwo z dalszej pespektywy. Zadać sobie pytania jakich informacji potrzebujemy, żeby ulepszać procesy – nawet te, które obecnie się nam sprawdzają.
Na przykładzie działu produkcji i utrzymania ruchu, możemy zwrócić uwagę np. na:
OEE (Overall Equipment Effectiveness) – całkowita efektywność wyposażenia.
- Przepustowość – średnia liczba jednostek produkowanych na maszynie, linii lub zakładzie w określonym czasie.
- Wielkość – ilość towaru wyprodukowanego w określonym czasie.
- Dostępność – stosunek czasu pracy do planowanego czasu produkcji.
- Wykorzystanie zdolności – wskaźnik całkowitej zdolności produkcyjnej wykorzystywanej w danym czasie – poziom wykorzystania mocy produkcyjnej w zakładzie.
- Produkcja w toku – ilość czasowo ukończonych produktów.
- Zużycie mediów – poziom konsumpcji energii elektrycznej, wody i innych mediów, można ilustrować je
w ujęciu jednego działu, linii, maszyny czy zakładu. - Koszt energii – wskaźnik całkowitego kosztu energii zużytej w danym okresie, podzielony przez ilość produktów wytworzonych w tym czasie.
- Braki produkcyjne – ilość produktów przeznaczonych do utylizacji z powodu wad produkcyjnych.
- Wydajność – wskaźnik Yield – to procent produktów, które zostały wytworzone zgodnie ze specyfikacją (iloraz z liczby jednostek wychodzącą z procesu, a z niego wychodzących).
- Zwroty – ilość klientów, którzy odrzucają nasze produkty, reklamując je.
- Czasu przestoju – czas, w którym proces produkcyjny nie jest realizowany.
Wskaźników, które możemy uznać za zasadne do pomiaru i monitorowania, jest wiele. Jednak jak wybrać te, których monitorowanie i analiza przynosi największe korzyści? Z naszego doświadczenia, z zakresu tworzenia systemów wspomagających pracę firm produkcyjnych i usługowych, możemy wyróżnić te, które sprawdzają się najlepiej, jako wskaźniki dla działu UR pomagające doskonalić i utrzymywać produkcje na światowym poziomie.
- Dostępność techniczna – jako element potrzebny do wyliczenia całkowitej efektywności wyposażenia, określa stosunek czasu operacyjnego (gotowości do działania) do czasu, który jest rozpatrywany w kontekście wykonania danego zadania.
- MTBF – średni czas pomiędzy awariami, jeden z podstawowych wskaźników określających częstość występowania awarii i rozumiany jest jako średni czas pracy pomiędzy wykonaniem prac naprawczych, w przypadku wystąpienia jednej awarii do drugiej, w określonym czasie.
- MTTF – średni czas do wystąpienia awarii – przedstawia średni czas pracy urządzenia od początku eksploatacji (lub zakończenia ostatniej naprawy) do wystąpienia awarii.
- MTTR – średni czas do zakończenia naprawy – określa czas trwania rzeczywistej naprawy od momentu zgłoszenia awarii do chwili zakończenia działań naprawczych.
Jakie efekty wnosi wykorzystanie wskaźników?
Po co mierzyć skoro wszystko działa… Jakie korzyści niesie ze sobą obliczanie i analiza ww. wskaźników? Przede wszystkim wyniki „wyłożone kawę na ławę” mogą uświadomić nas, że jednak utrzymanie ruchu nie działa tak dobrze, jak wydawało nam się przez dłuższy czas, a nawet jeśli przedstawione dane są satysfakcjonujące – jak możemy zwiększyć efektywność działów, przy czym osiągnąć wyższy zysk.
Korzyści wynikające z obliczania wskaźników:
- Łatwość w ustaleniu krytyczności maszyn i priorytetów działań,
- Trafność planowania czasu przeglądów oraz prewencyjnych wymian kluczowych części na maszynach,
- Wzrost skuteczności działań służb Utrzymania Ruchu – wskaźnik MTTR maleje = średni czas usuwania awarii skraca się,
- Zmniejszenie marnotrawstw,
- Łatwość określenia postępów przy wdrażaniu działań Automonous Maintenance.
Jak pomagają systemy informatyczne?
Wraz z chęcią analizy wskaźników i wykorzystania ich w celu doskonalenia procesów firmowych, może brakować rąk do pracy, by wszystkie pomiary spisywać, odpowiednio obliczyć i analizować. Wtedy z pomocą przychodzą systemy informatyczne, które jako jedną ze swoich funkcjonalności oferują raporty zawierające interesujące nas dane. Co ważne, wykorzystują dane, które pracownicy na bieżąco wprowadzają do systemu, dzięki czemu są samowystarczalne przy wyliczaniu wartości wskaźników. To co pozostaje nam do zrobienia to celna interpretacja i wprowadzanie udoskonaleń. Jednak czy system przedstawia je nam w łatwy do analizy sposób, tak abyśmy mogli osiągnąć zamierzone korzyści? Czego system potrzebuje, aby wskazać nam prawidłowe wyniki na ekranie monitora?
W celu wykazania dostępności maszyn w zakładzie system gromadzi informacje o wystąpieniu awarii wraz w przypisaną do konkretnego incydentu maszyną. Rejestruje datę i czas trwania zatrzymania pracy maszyny oraz opis awarii, wprowadzony przez pracownika. System przedstawia wynik dostępności maszyn, rozgraniczając czasy zatrzymań na awarie i przeglądy, co przekazuje nam dokładniejsze informacje o pracach trwających w dziale.
Wskaźnik MTBF wyliczany jest dzięki poprawnej rejestracji czasu pracy przez techników. Jeśli wszystko się zgadza, system wyświetli nam średni czas pomiędzy naprawami wraz z czasem pomiędzy wystąpieniem awarii (od wystąpienia 1 awarii – do 2 awarii), oraz opisem aktualnej awarii wraz z poprzednią – co pomaga nam lepiej identyfikować powód występowania przestojów.
Kierujemy się zasadą MTTF + MTTR = MTBF.
Podobnie przedstawiany jest wskaźnik MTTF, jednak żeby średni czas do wystąpienia awarii przedstawiany był w jak najdokładniejszy sposób, potrzebujemy gromadzić dane historyczne, które w tym przypadku mają szczególną wartość. Warto pamiętać, że jeśli w danych okresie czasu nie wystąpiła żadna awaria, z czego wynika – brak naprawy, system korzysta z podanego okresu czasu, np. początek eksploatacji maszyny.
Średni czas naprawy – wskaźnik MTTR, obliczany jest przy pomocy czasu zarejestrowanego przez poszczególnych techników, jaki spędzili przy konkretnej naprawie – dokładną rejestrację, a co z niej wynika – dokładną wartość wskaźnika, ułatwiają jednostki mobilne, dostępne w systemach, jako moduły dla techników.
Co ważne kilka elementów, które pracownicy rejestrują przy pomocy jednostek systemowych, pomaga automatycznie wyliczać nie tylko wskaźniki efektywności działu produkcji czy UR, możemy z nich czerpać dane potrzebne przedstawiać pozostałe raporty, takie jak PARETO lub krytyczność . Dlatego pamiętaj, wdrożenie systemu usprawnia wiele aspektów pracy twojego przedsiębiorstwa, od przyśpieszenia działań wykonawczych, po analizy i rozwój całej firmy.